Dual Furance
A dual track induction furnace is a type of induction furnace that features two separate tracks or channels for melting and holding metal. It is designed to provide efficient and continuous melting and holding capabilities for various alloys.
In a dual track induction furnace, the upper case is refractory lined and houses the molten metal. It is divided into two separate channels or tracks. The induction unit assembly, known as the lower case, is attached to the upper case via a throat and provides the melting or holding power.
The dual track furnace operates on the principle of a transformer, similar to a core-type induction furnace. An alternating current flows through a primary coil that surrounds an iron core. The molten metal in each track forms a secondary coil, which surrounds both the core and the primary coil. As the current flows through the primary coil, it induces a larger current in the secondary coil, generating heat through the Joule Effect.
The dual track induction furnace allows for simultaneous melting and holding of different metals or alloys in separate tracks. This enables efficient production processes and reduces downtime between melting and holding cycles. The molten metal in each track circulates within the upper case, creating a beneficial stirring action that helps achieve uniform temperature distribution and alloy homogeneity.
Overall, the dual track induction furnace is a versatile and efficient tool for melting and holding various metals and alloys. It offers flexibility in production processes and ensures high power efficiency through the concentration of magnetic flux in the metal loops.
Upgrade your foundry operations with IPM dual track induction furnace! Maximize efficiency and productivity with simultaneous melting of different metals or alloys. Our innovative design reduces downtime and offers flexible operation for your metal casting needs. Contact us today to elevate your foundry to the next level!
Induction furnace is used for smelting or insulating ferrous metals, non-ferrous metals, sponge iron, such as scrap iron, scrap steel, copper, aluminum and so on. Complete working equipment such as continuous casting machine, rolling mill, mainly used for the production of billet, steel bar, angle steel, H-beam, I-beam, etc. Using KGPS, IGBT, single or double power supply technology, PLC (Siemens) can be realized throughout the monitoring.
Main supply list: 2 sets of electric furnace body, 2 sets of hydraulic or mechanical tilting electric furnace mechanism, 1 set of control platform, 1 set of intermediate frequency control cabinet (6 pulse 1, 12 pulse 2, 24 pulse 4), low voltage control cabinet (6 pulse 1, 12 pulse 2, 24 pulse 4), 1 set of capacitor cabinet, 4 or 8 water-cooled cables; 1 water temperature alarm, 1 leakage alarm; 1 crucible mold, 1 liquid One batch of pressure steel pipe, one set of copper row, three water tanks. Transformer, cooling tower, furnace builder, furnace lining ejector, furnace cover.
Product Model: GW1.5-IGBT-1300-0.5-BDual output with a set of power supply, can supply power to two sets of furnaces simultaneously, to achieve “one for two”, total power can realize stepless free distribution on two sets of furnaces. Equipping two sets of furnaces, one is used for melting or heating refining , the other is used for insulation and casting, and two sets of furnaces can mutual replace to use. Medium frequency power supply device of IGBT transistor module can be used for melting, induction heating, heating treatment.
DUAL / MULTI MELTING SYSTEM
- Single Induction Power Supply Having Multiple Outputs
- Melt or Hold in DUAL OR MULTIPLE Furnaces at the same time.
- Automatic Maximum Power control.
- Operator can increase or decrease the power to the required furnace.
- Very useful for the foundries.
- Furnace utilisation factor can be increased to 95%
- Simple Plug and Play Installation.


DUAL CONTROL
- Independent control for each Furnace.
- Independent Instrumentation for the each furnace.
- Common Instrumentation for the Input Power.
- Automatic power Sharing as demanded by the operator.
- Common Computer with multiple options for operator.
Releated Products
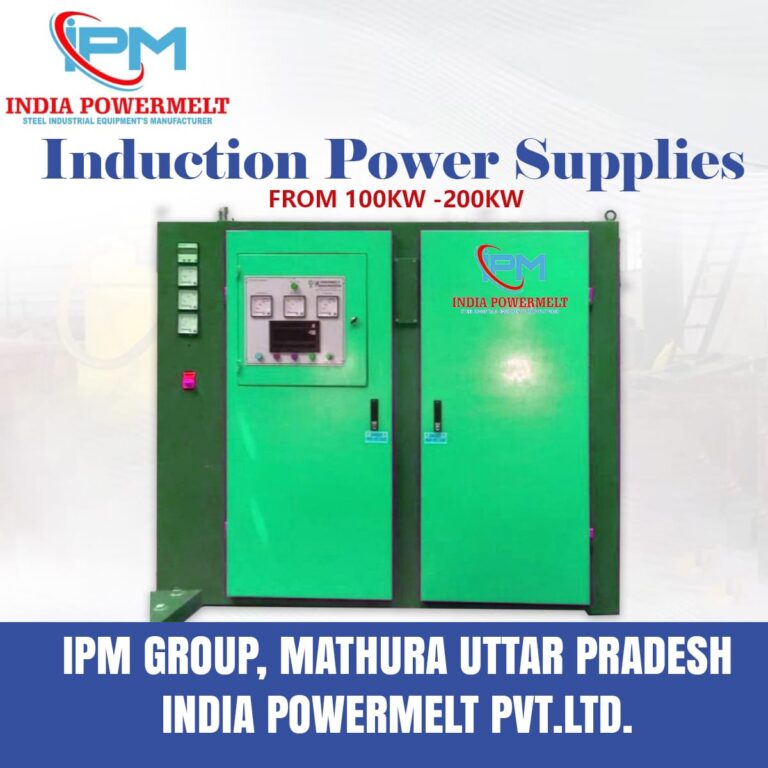

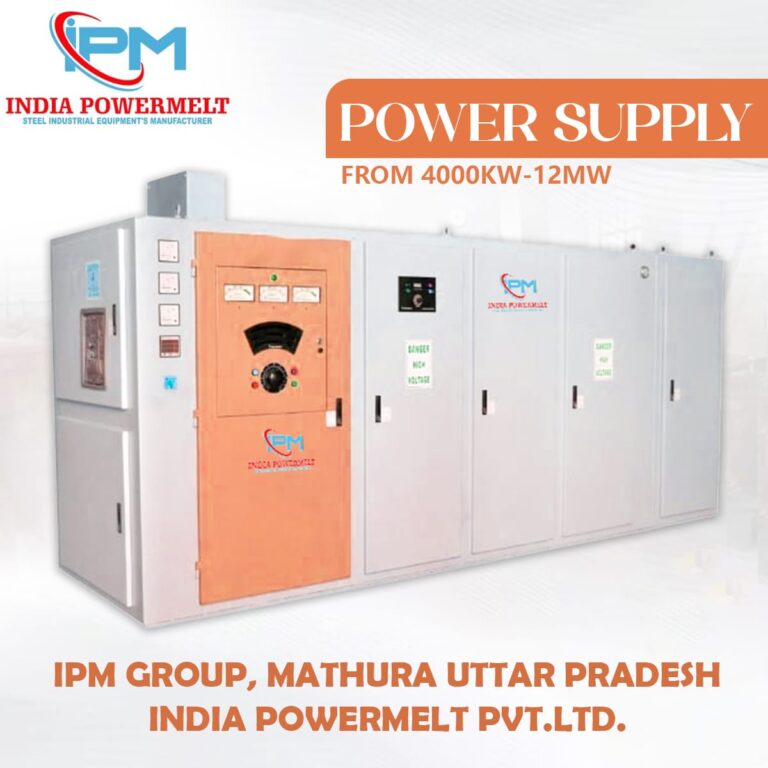

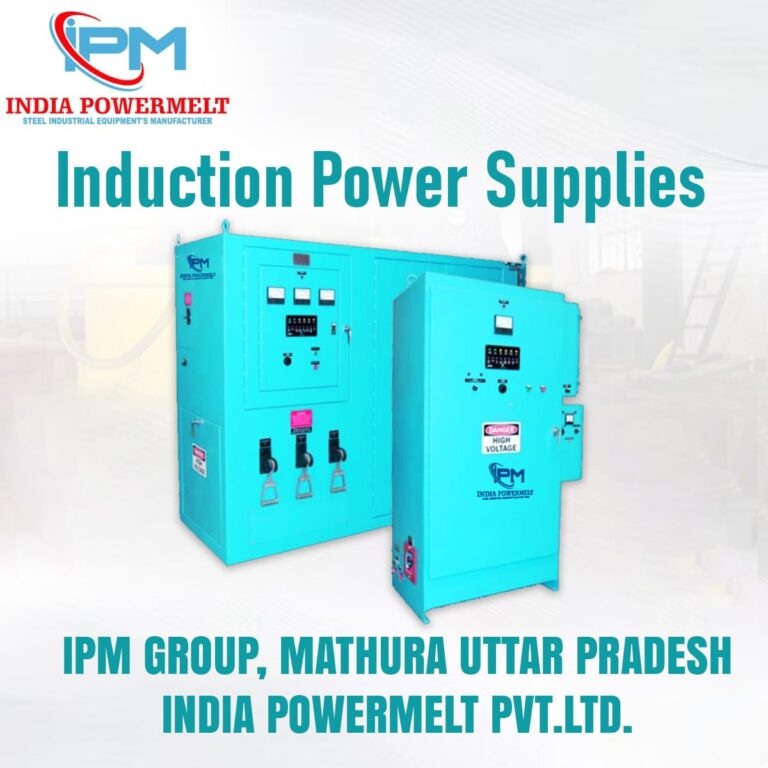

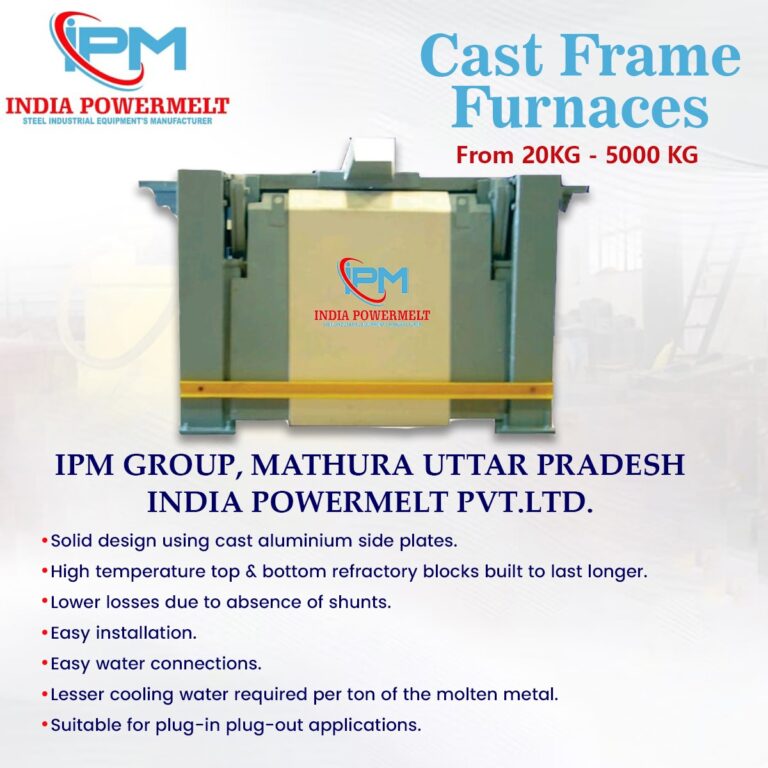
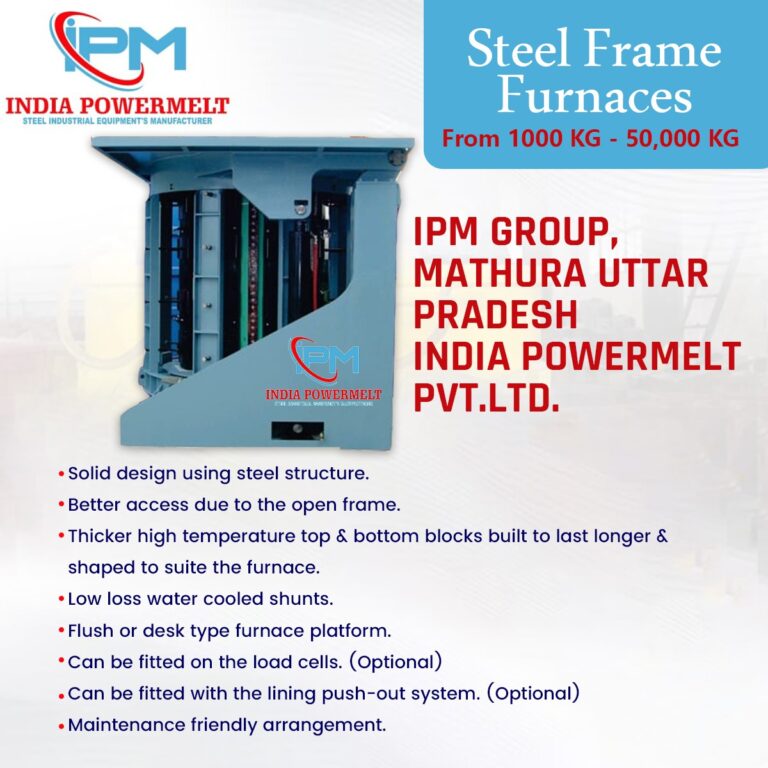
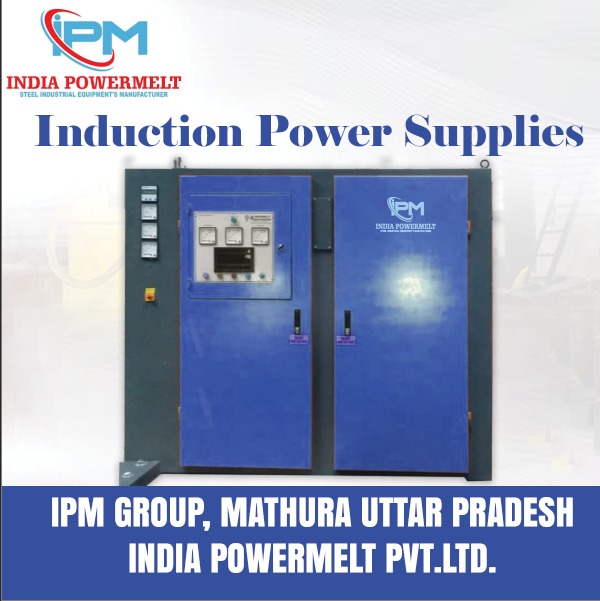