Beam Blank Casting
BEAM-BLANK CASTING REDUCED
In the last years, India Powermelt Technologies has developed and implemented near-net-shape beam blank casters and special designed combi-caster for long products, which offer the operator highest flexibility with respect to different casting sections and market demands. It is possible to combine the production of billet, bloom and near-net-shape beam blank at one single casting machine. An optimization for beam blank casting has been reached with latest developments in the equipment design and in the fine tuned mold tapers and spray cooling. India Powermelt Technologies beam blank casters provide high productivity combined with direct hot charging to the rolling mill. Near net shape beam blank casting is an excellent alternative to the more conventional bloom casting route for the production of small to jumbo H-beams and profile shapes.
Main benefits
- Increase of production and flexibility
- Optimum performance and availability
- Assurance of optimized solutions for unique and specialized requirements
- Maximum system and plant availability at low maintenance costs
ELECTRICS AND AUTOMATION FOR CONTINUOUS CASTING
Sophisticated automation packages are prerequisite for state-of-the-art quality steelmaking. India Powermelt Technologies has always been a driver of innovation in this area, especially also providing expert technological packages and models that cover all aspects of the continuous casting process.
The well proven Lev Con mold level control package adapts reliably and extremely quickly to mold level fluctuations and changing casting conditions. This is made possible by advanced model-based control algorithms that can actually look into the near future to avoid disturbances in the control loop. The intelligent interaction between the advanced software and highly robust mechanical components improves safety and brings plant operators one step closer to fully automatic casting operation.
Further highlighted technological packages and process experts:
- Dyna Flex: hydraulic Oscillator for perfect surface quality
- Quality Expert: a milestone in improved quality supervision, quality prediction and control
- Yield Expert: cut length/weight optimization for minimized scrap and optimized yield
- Dyna Speed: advanced secondary cooling solution
- Nozzle Expert: highest accuracy in detecting clogged nozzles and broken hoses
- Speed Expert: optimal casting speed for increased throughput and improved quality
TECHNOLOGY AND MODERNIZATION PACKAGES
Name | Short Description |
---|---|
Mold Expert Fiber | Live view into caster mold based on fiber optic technology |
Scrap Torch Cutting Machine | Environmentally clean scrap processing |
CC Optimizer | Process optimization (Level 2) for continuous casting |
Dyna Flex | Hydraulic mold oscillator for continuous casting |
Lance Checker | Test and diagnosis system for liquid iron and steel measuring devices |
Lev Con | Mold-level control with highest precision for continuous casting |
Liquirob for Casting | Robotic solution for continuous casting machines |
Mold Expert | Breakout pre-detection and mold monitoring |
Oscimon | Online monitoring of mold oscillation in continuous casting machines |
OscicChecker | Portable device for mold oscillation measurement in continuous casting machines |
Beam-blank sections range from 250 to 1,150 mm wide, and from 150 to 500 mm high. The largest beam blank section currently in use has a height of 490 mm, a width of 1’150 mm and a web thickness of 130 mm. This called for completely new approaches in terms of the design and dimensions of the molds as well as the entire set-up of the continuous casting equipment.
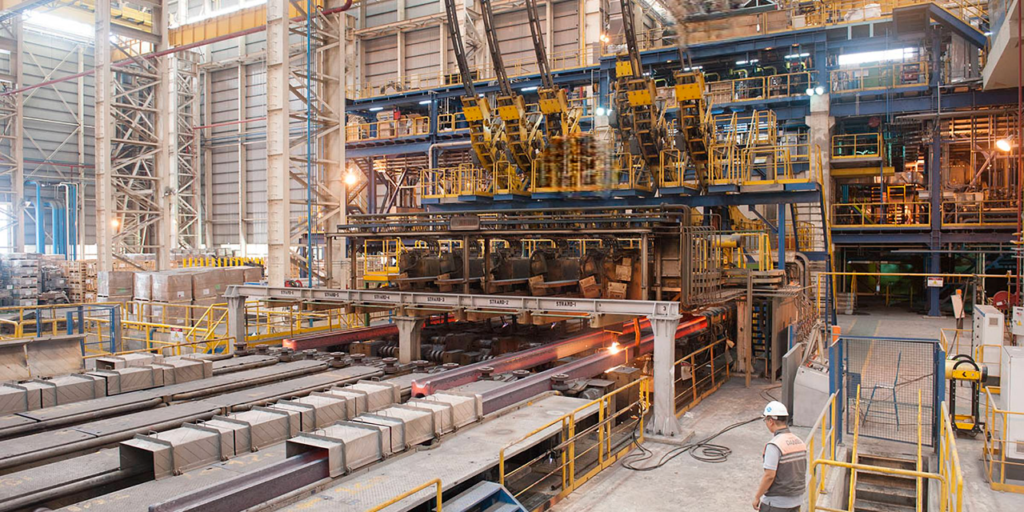
Materials | Carbon grades for light, medium, heavy section rolled beams (incl. wide flanged beams) |
---|---|
Section sizes (height x width x web thickness) | 150x150x100mm to 1150×490 x130 mm |
Casting Radius | 9-12 m |
Nbr of strands | 1 to 8 |
Casting type | Closed (powder) for SBQ and open (oil) for rebar |
Casting Speeds | 2 up to 4 m/min |