Hot Rolling Mill
Hot Rolling Mill
INDIA POWERMELT provides Design, engineering, and manufacturing of Complete Turnkey Solutions of Rolling Mills with over 15 years of experience. Our Design team works towards continuously improving the processes, products, and tailor-made solutions services in various industrial sectors. Extensive service knowledge gives us the privilege to understand your needs in advance; driving the market trends with new solutions like Cost reduction, process improvement, and efficiency to name a few. Our Rolling Mill plants give you what you need to respond flexibly to market demands. We work endlessly to provide you the best solutions for hot rolling mills which provide high productivity and cost-effectiveness.
INDIA POWERMELT implements the entire range of project engineering for your Rolling Mill from conceptual and detailed design to construction and start-up engineering. Depending on your final products and production volume, we develop custom solutions especially for you across the globe. These range from completely new plants to modernizations and service schemes for existing equipment.
From bar mill to section mill, from chimney to complete reheating furnace, from roll stand and water quenching system to complete rolling mill train, from cooling bed area to bar/coil handling area, from flying shear to cold shear, full Automation System and from engineering services to turn-key plants India Powermelt is the one-stop solution for all your Rolling Mill needs.
Rolling Mill Manufacturers
We provide Rolling mills capable of producing Bar rods from sizes 8 to 40 mm with the production capacity ranging from 75000 to 500000 TPA.
The Bar rods are made with Billets/Ingot which passes through various stands to get the desired shape and size. The bar then passes through the quenching system and gets self-tempered and quenched. The process is undertaken to increase the strength of the rebars.
The Rolling mill comprises the following process flow:
1.Rolling Mill Train
A) Rolling Mill Train – Equipment– All mechanical equipment incorporates the latest known and proven technology.
Finishing Line mill stands are Housing less series, which are very well known worldwide for their rigidity and easy maintenance. The “housing less” stands can be used for producing all grades of steel including stainless high speed and high alloy steel. Special “robots”, in the stand preparation shop, are used for quick roll changing thus reducing the requirement for costly spares and stand-by equipment.
All the rolling mill stands are individually driven by DC motors and the rolling process will be in tension control in the roughing and intermediate mills, while in the finishing stands will be no-tension control using loopers.
Crank and flying shears are provided to remove the oversize head of the bar as it progresses down the rolling line. This feature ensures easy entry into the rolling mill stands and minimizes cobbles. As you can note the offered stands are divided into four main size groups. The main advantages of this solution are:
B) Rolling Mill Train – Roll Pass Design – The roll pass design has to reduce to the minimum the investment in rolls and consequently the operation cost and, moreover, to allow high productivity and high final quality of the products. The main characteristics of the proposed roll pass design are:
2. Quenching System: After leaving the finishing stands, to improve the mechanical properties of the deformed bars, an in-line water quenching system is foreseen. The main benefits that we can have with this system are High yield strength of the material, Better weldability of material, Lower cost of material, High plasticity of bars after treatment, and Better stiffness of the bar.
3. Cooling Bed: Just after rolled, the bars are subdivided by a flying shear in multiple commercial lengths and sent to the cooling bed onto a roller table provided with aprons. The electrically driven mobile elements break the rolled stock materials and discharge them onto the racks of the cooling bed. A series of fixed and moving rakes are foreseen to collect and cool the bar coming from the roller table with aprons. The moving racks are operating automatically by the gear reducer start-stop drive. During their transport materials are cooled and discharged then onto chain transfer that shifts materials layer in the required number until take-out system provides to pick-up each layer of bars and laid them to the cooling bed run-out-roller table to feed the final commercial cold cut line.
4.Run-Out Roller Table: The system is provided to keep in position the layer, made on the pitch-to-pitch chain transfer at the cooling bed exit, during its transferring onto the run-out roller table.
5.Cold Cutting to Length Area: The final cold cutting operation will be performed by means of the Cold Static Shear. This machine, for such type of profile, is the most suitable for cut quality and in cutting costs. The shearing is performed by a pair of blades, one of which is fixed and the other mounted on a movable slide, which every time is started and stopped by an air-operated clutch/brake group by an AC motor.
6.Bundling Area: The bundling area consists of chain transfers for layer transportation and layer buffering(during bundling floatation) and finally chain transfer depositing the counted bars in the bundle forming area. The chain transfers system duty is to transfer the bar layers to the bundling area, and, when the bundle is informing position, to act as a buffer system.
7.Collecting Area: When the bundle is ready, by means of the adjustable roller table, it will be transferred to the tying area where the wire tying machine, hydraulically operated, will tie the bundle in the required numbers of ties. When the tying operation is finished, the bundle is transferred to the collecting area where it will be also weighed and labeled accordingly.
The specialty of our Rebars high flexibility and proven reliability. Our state-of-the-art Rolling Mills can manufacture an array of products like angles, squares, flats, channels, rounds, and wire rods. This top versatility also means you can efficiently produce all sizes, materials, and alloys.
We as a system supplier, offer you Mechanical Equipment clubbed with electrical and automation systems, plus technological expertise from a single source. That ensures the products you make in plants set up by us always make the grade in terms of both quality and efficiency.

Twin Channel
INDIA POWERMELT offering high grade TMT Twin Channel Manufacturing in India installed along entry side of the cooling bed to minimize the risk of accidents while transferring the bars. This carries the bar in a closed channel until the material comes to a standstill position and discharges it to the bed below automatically.
The basic and prime use of twin channel is to collect the TMT bars leaving the quenching boxes after being sheared by the flying shear in two strands.
The twin channels capable of guiding the discharge of the rods from dividing shear.
The twin channel is capable of collecting bars with size up to 40mm in diameter and have a maximum speed of about 25 meters per second.
The closed twin channels ensure that the bars do not come out and maintain safely of the people involved in the process. The opening and closing of the channels is done through cam-shaft and follower rollers.
The twin channels consist of alternatively opening flaps through a hydraulic cylinder and CAM system.
The bar enters the closed flap that opens when the full bar has been obtained. It has a free fall on the straightening pockets of the rake type cooling bed, which moves on the fixed & moving rakes to the mill run out table.
This is an excellent system because it carries the bar during a closed channel, minimizing the accident hazards. Specifically while completing high speed rolling the system is an absolute necessity.
Its design features makes it possible to figure in conjunction with braking pinch rolls, minimizing the length of run-in. The operations of twin channel are automated and are guided by the discharge of the rods from dividing shear. An innovative idea for cast iron center boxes has drastically brought down maintenance time.
Automatic Rake Type Cooling Bed
INDIA POWERMELT is engaged in providing supreme quality Automatic Rake Type Colling Bed Manufacturers in India that’s primarily used for purpose of naturally uniform air-cooling of TMT bars and transporting constant in an exceedingly phased manner.
This transporting is completed from the entry of the cooling bed to discharge facet. In this, the front end of the bars is additionally leveled at the discharge facet and a set range of bars area unit sent for final length cutting by cold shear and bundling.
The mechanism of our cooling bed assures that the bars area unit uniformly positioned over the toothed racks. Our Colling Bed Manufacturers is meant considering the finishing mill stand of the mill and cooling time needed for the varied sizes of the bar.
COMPLETE SYSTEM COMPRISES
Fixed Grid
Straightening rakes comprising forged iron toothed blocks that assist in receiving bars and straightening it at temperature of around 600o C
Moving rakes
Movable rakes mechanism to maneuver in ‘X’ and ‘Y’ axis which can be profile move suit smallest size yet as most bar size. Drive for movable rack mechanism comprising motors driving 2 parallel sets of drive shafts.
Fixed Rakes
Fixed Rakes mechanism that receives bars from movable rack mechanism are being transferred toward delivery facet of cooling beds.
Aligning roller
Bar orientating rollers fitted at finish of racks and driven by motors for orientating bars front end before delivery to run-out roller table. We have many location wherever our Automatic Cooling Bed is running with success.

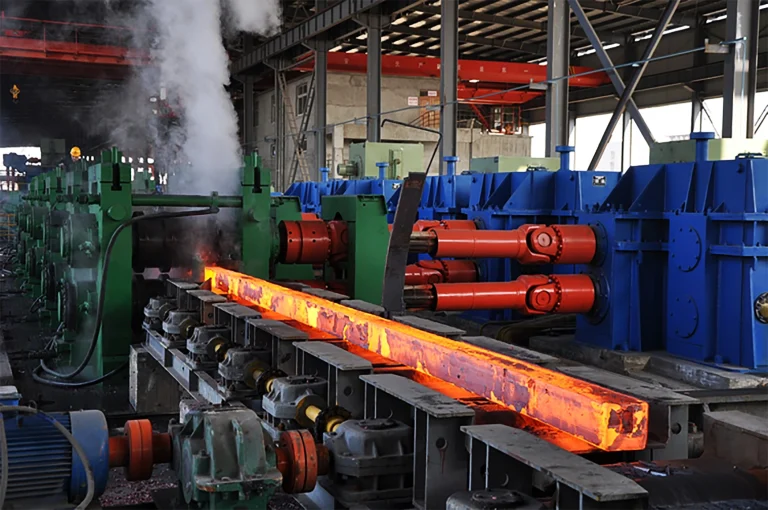
Bar Bundling & Bending System
INDIA POWERMELT is one of the leading supplier company of TMT Bar Handling System Manufacturer industry all over the world. We manufactures a top range of Bar Handling System in India which automates the rolling mill plant till the end product. Our Company makes TMT Bar Handling Systems, bar counting system, bar bending system, bar tying or bundling system also.
We are a high standing supplier company, recognize for its quality within the steel industry.
INDIA POWERMELT designs technical upgraded Chain Transfer Systems, which are installed at the side of run out roller table once the cold shear.
In this, the first chain set cuts across the run out roller table once the cold shear. It has its resting on the common tie bar, which is fixed with the gas (pneumatic) cylinders. The cut bar heap within the system received on the run-out roller table, wherever the chains set lifts.
Bar Handling Area
Finishing machines includes the automatic staking, bundling, binding, weighing and labeling of rolled products.
Stacker and Building Systems
Stackers offers handling of straight and reverse layers for all type of sections. Mechanical handling or Magnetic handling of the straight and reverse layer with high stacking cycle performance. Stackers offer built-in bundling operate. Bundlers for round and flat bars are available together with bar counting for rounds and small bundle processing systems. The packing form can be round, square, rectangular and hexagonal.
Binding Systems
Automatic binding of the packages and bundles is available here with wire or strapping.
Weighing & Labeling
All bundles can be automatically weighed and further labeled for quality assured delivery of the completed products.

Automatic Bundling Machine
Automatic Bundling Machine finds utilization in wire rod Steal Plants for folding bundle of TMT Bars & Steel bars. The Automatic Bending Machine meet the needs of bundling and packaging hexagon, square, round rods and tubes. Other than this, these additionally meet the needs of bundling spherical and flat bars.
Features
- Available with option of bar counting for rounds.
- Can be designed to manage bundles of special weight and size capacities.
- System designed for effortless handling of the material.
- Provides for most utilization of handy space.
- Allows bundling to be achieved as per necessities in multiples of metric tonnage.
- Provides for impervious bundling that makes the merchandise effortless to transport as nicely as assist in averting pilferage possibilities.
- Bar Bundling machines on hand in distinct capacities as per customer’s requirements.
- The computerized operations offers for making use of uniform strain at ordinary intervals that end result in attaining uniform bending operations.
- Helps in keeping bar electricity that in any other case receives disturbed through guide process.
- Allows for any bend, angle or stirrups to be made.
- Superior lubrication assist that eliminates requirement for routine maintenance.
- Bars bundled are loaded into machine in bulks of 1 ton.
Operations Performed
- Accepting threaded Rods that are loaded the usage of overhead crane.
- Feeding of the threaded rods.
- Aligning threaded rods to make certain these are flawlessly square.
- Transferring bundles to wrapping station.
- Wrapping bundles by way of rope/welded plastic strips.
- Discharge bundle into completed bundle bin.

Available packaging forms :
The packing form can be in form of:
- Round
- Square
- Rectangular
- Hexagonal
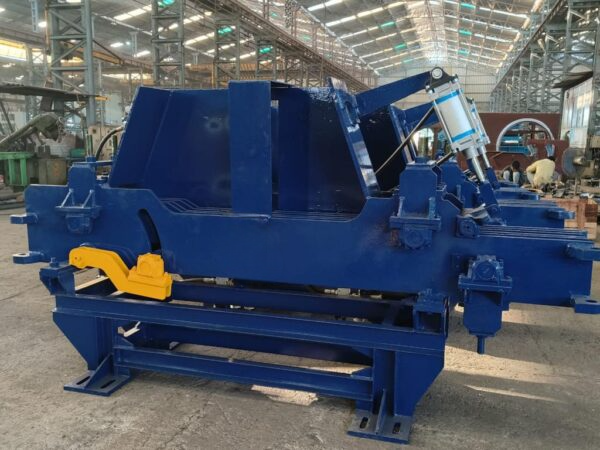
Loopers
For optimized rolling between stands, loopers maintain a loop to ensure that there is no tension in the rolled material. Looper and tension control is important in hot strip mills because they affect the strip quality as well as strip threading.
INDIA POWERMELT make both, Horizontal loopers and Vertical Loopers along with Necessary instrumentation like loop scanners and automation.
Horizontal Looper
Horizontal loopers store strip on a horizontal rotary table. Where the space is available this is the most efficient and cheapest method of storing strip without causing any surface damage. Like Spiral Accumulator and the Free Loop Accumulator.
Vertical Looper
Loopers works with Automatic Sensor called LOOP SCANNER. It is an electronic device which accurately measures the size of the loop on wire, rod and profile mills, even for special metals, and in the presence of steam and fumes.

